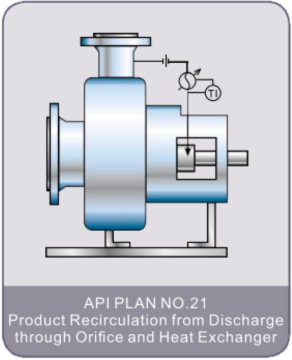
API Plan 21
Overview:
- In API Plan 21 the pumped fluid is recirculated from the pump discharge, through a flow control orifice and heat exchanger, and injected into the mechanical seal.
- The heat exchanger, also referred to as a “seal cooler”, can be either water or air cooled.
Advantages:
- Self-venting
- API Plan 21 provides cooling of the process fluid which is then used to lubricate and cool the mechanical seal.
Best For:
- Hot applications
- Lowering the vapor pressure margin of the pumped fluid
- Clean process fluids – free of contaminants and abrasives
- Process fluids not susceptible to polymerization or “setting-up” at ambient or lower temperatures
Best Practices:
- Orifice size should be no less than 1/8 in. (0.125 in.)
- Calculate the pressure differential between the pump discharge pressure and the seal chamber pressure to ensure positive flow into the seal.
- Isolation valves should not be installed in the Plan 21 flush piping. If such a valve is installed in the flush line, there poses the risk of it being closed and preventing flow to the seal. In such an event, the seal life will be drastically reduced and subsequently fail due to the lack of cooling and lubrication.
- Routine Maintenance
- Record the temperature of the following. Compare to previous records to trend performance.
- Process fluid into heat exchanger
- Process fluid out heat exchanger
- Cooling water into heat exchanger
- Cooling water out heat exchanger
- Backflush the heat exchanger at least monthly. If cooling water quality is poor, backflush the heat exchanger weekly or more frequently based on operating experience. Backflushing the heat exchangers will help prevent and mitigate fouling and clogging within the heat exchanger.
- Record the temperature of the following. Compare to previous records to trend performance.