Last Updated: 12/18/2023
Mechanical seals play a crucial role in maintaining the integrity of rotating equipment, preventing leaks, and ensuring efficient operations. However, like any mechanical component, seals are susceptible to wear and tear, which can lead to failure if not addressed promptly. In this blog post, we’ll explore the common signs of mechanical seal failure and provide insights into how to effectively address these issues.
Signs of Mechanical Seal Failure:
Leakage:
- One of the most obvious signs of mechanical seal failure is leakage. If you notice any fluid escaping from the seal area, it’s a clear indication that the seal is compromised. It’s crucial to identify the source of the leak promptly.
Unusual Vibrations:
- Excessive vibrations can indicate misalignment or damage to the mechanical seal. Regular monitoring of vibration levels and trends can help detect potential issues before they escalate.
Increased Operating Temperature:
- A sudden rise in the operating temperature of the equipment may suggest friction and increased wear within the mechanical seal. Monitoring temperature trends can provide early warnings of potential seal failure.
Fluid Contamination:
- If you observe contamination of the process fluid, such as the presence of particles or discoloration, it could be a sign that the mechanical seal is allowing external contaminants to enter the system.
Abrasive Wear and Scoring:
- Inspecting the sealing faces for signs of abrasive wear or scoring is crucial. These visual cues may indicate that the seal is not functioning correctly and is experiencing excessive friction. It is important to conduct failure analysis for each mechanical seal failure and to ensure corrective actions are taken. These measures alone will greatly improve the life and reliability of both the seal and equipment.
Addressing Mechanical Seal Failure:
Perform Regular Inspections:
- Implementing a proactive maintenance schedule that includes regular inspections of mechanical seals is essential. Look for signs of wear, corrosion, and other damage during these inspections.
Monitor Seal Environment:
- Understanding the operating conditions and the environment in which the mechanical seal operates is crucial. Ensure that the seal is compatible with the process fluid and that environmental factors, such as temperature and pressure, are within specified limits.
Proper Installation and Alignment:
- Incorrect installation and misalignment can significantly contribute to mechanical seal failure. Follow manufacturer guidelines for installation and alignment to prevent premature wear and damage.
Use Appropriate Seal Materials:
- Selecting the right materials for the mechanical seal based on the nature of the process fluid is critical. Incompatible materials can lead to chemical attacks, erosion, and degradation.
Regularly Replace and Upgrade Seals:
- Mechanical seals have a finite lifespan, and regular replacement is necessary to avoid unexpected failures. Consider upgrading to newer seal technologies that may offer improved performance and reliability. Consider upgrading from a component seal to a cartridge seal.
Detecting signs of mechanical seal failure early on is crucial for preventing costly downtime and equipment damage. By implementing proactive maintenance practices, monitoring operating conditions, and addressing issues promptly, you can ensure the longevity and efficiency of your rotating equipment. Regular collaboration with manufacturers and industry experts can also provide valuable insights into the latest advancements in mechanical seal technology, helping you stay ahead of potential challenges. Remember, a well-maintained mechanical seal is the key to the smooth and reliable operation of your rotating equipment.
Have questions? Contact us today for expert guidance and personalized solutions to address your inquiries.
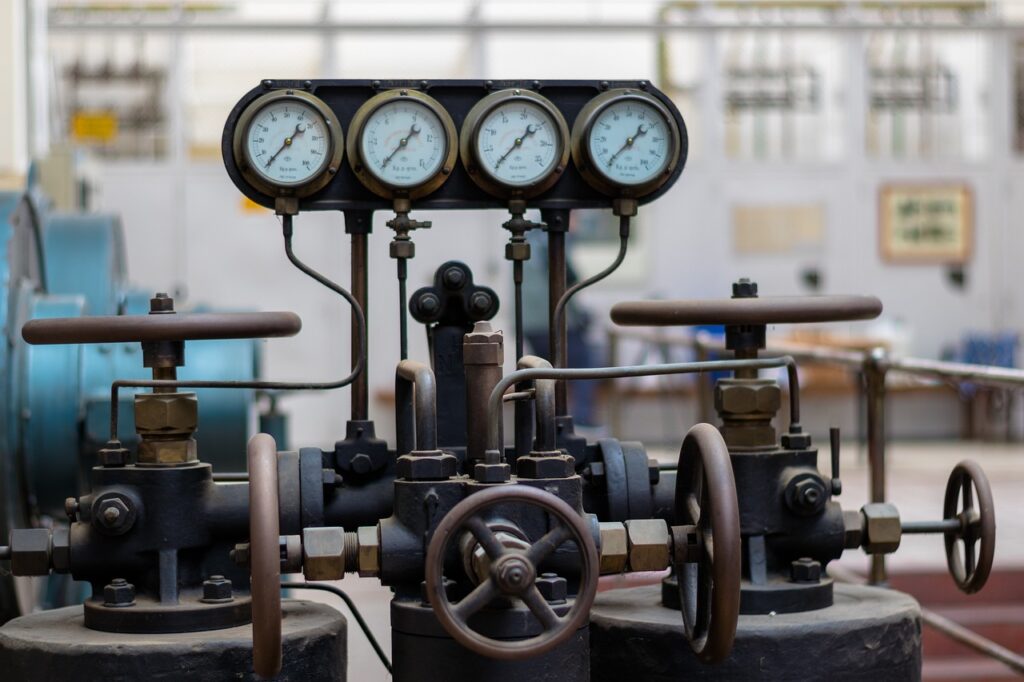