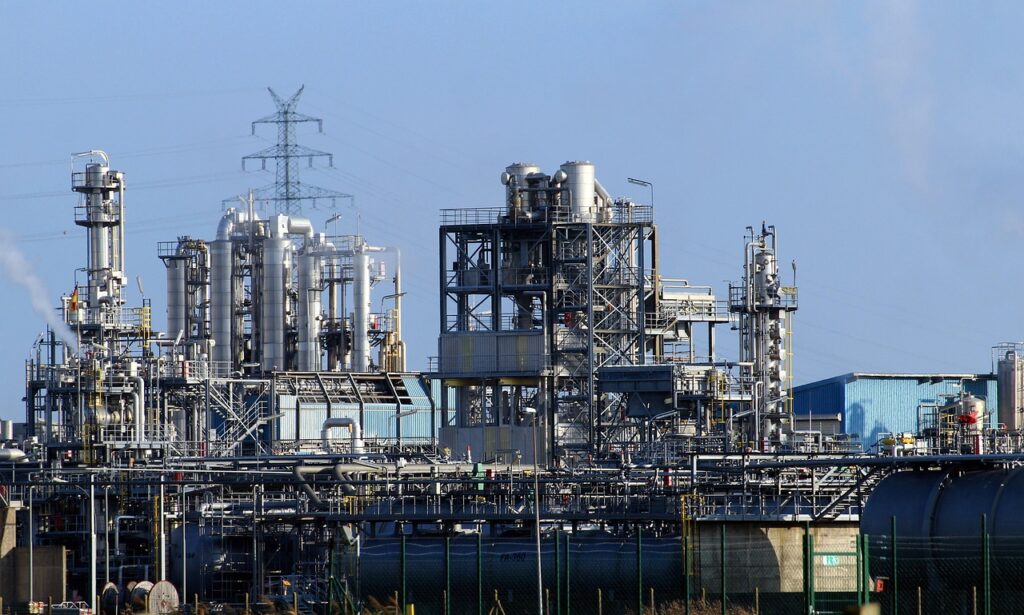
Last Updated: 12/11/2023
In the realm of rotating equipment, the reliability of every component is paramount to the seamless operation of industrial processes. Mechanical seals, often inconspicuous but undeniably essential, play a crucial role in maintaining equipment reliability and minimizing downtime. In this blog post, we’ll delve into the impact of mechanical seals on equipment reliability and explore how their proper functioning can significantly reduce costly downtime.
Guardians Against Leaks:
Mechanical seals act as vigilant guardians, preventing leaks that could lead to fluid loss and equipment damage. The consequences of leaks extend beyond immediate operational disruptions, encompassing environmental concerns, safety hazards, and financial implications. A reliable mechanical seal forms the first line of defense against these challenges, enhancing overall equipment reliability.
Mitigating Environmental Impact:
The environmental impact of equipment failures goes beyond the immediate operational concerns. Leaks resulting from seal failures can lead to the contamination of soil, water, and air. Mechanical seals, by preventing such leaks to the atmosphere, not only ensure equipment reliability but also contribute to environmentally responsible practices, aligning with modern sustainability goals.
Compatibility with Harsh Environments:
Many industrial processes involve challenging environmental conditions, such as high temperatures, corrosive chemicals, or abrasive materials. Mechanical seals, when appropriately selected for the application, exhibit resilience in harsh environments. Their ability to withstand these conditions enhances equipment reliability, especially in industries where challenging operating environments are the norm.
Sealing the Deal on Safety:
Beyond reliability and downtime considerations, mechanical seals contribute significantly to safety in industrial settings. By containing hazardous fluids and preventing leaks, these seals create a safer working environment for personnel. This dual benefit of enhancing safety and reliability underscores the critical role that mechanical seals play in overall industrial operations.
Friction Reduction for Longevity:
Excessive friction within rotating equipment can accelerate wear and compromise the lifespan of critical components. Mechanical seals, when compared to pump packing and when properly installed and maintained, contribute to friction reduction. The cartridge design of a mechanical seal (e.g. single cartridge seal) also prevents wear on the rotating equipment by wearing the seal parts, rather than the pump parts (i.e. shaft, etc.). By creating a barrier between moving parts, these seals mitigate wear and extend the operational life of the equipment, thereby enhancing overall reliability.
Preventing Unplanned Downtime:
Unplanned downtime can be a significant source of financial loss for industries. Mechanical seals, as preventive components, play a crucial role in averting unforeseen failures. Regular maintenance and monitoring of seals help identify potential issues before they escalate, allowing for timely interventions and reducing the likelihood of unexpected downtime. Examples of routine monitoring include vibration monitoring and thermographic scanning.
Proactive Maintenance for Peak Performance:
A proactive maintenance approach, including regular inspections and replacement of seals as part of a scheduled maintenance program, is key to sustaining equipment reliability. By identifying wear or potential issues early on, maintenance teams can address concerns before they escalate, ensuring that mechanical seals continue to perform at their best. A good maintenance program also includes a root cause failure analysis (RCFA) to determine how and why the seal failed.
Mechanical seals may be small components in the grand machinery of industrial processes, but their impact on equipment reliability and downtime reduction is indisputable. As industries strive for efficiency, safety, and sustainability, recognizing the significance of these seals becomes imperative. A strategic focus on proper installation, regular maintenance, and selecting the right seals for specific applications can collectively contribute to a robust foundation of reliability, minimizing downtime and fostering smooth, uninterrupted industrial operations.